References
Clients who trusted us:
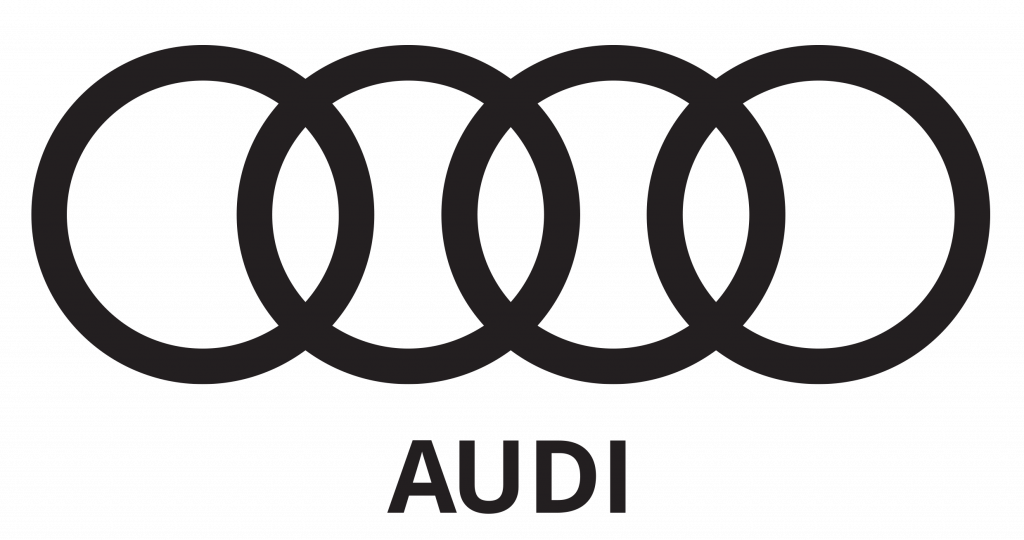
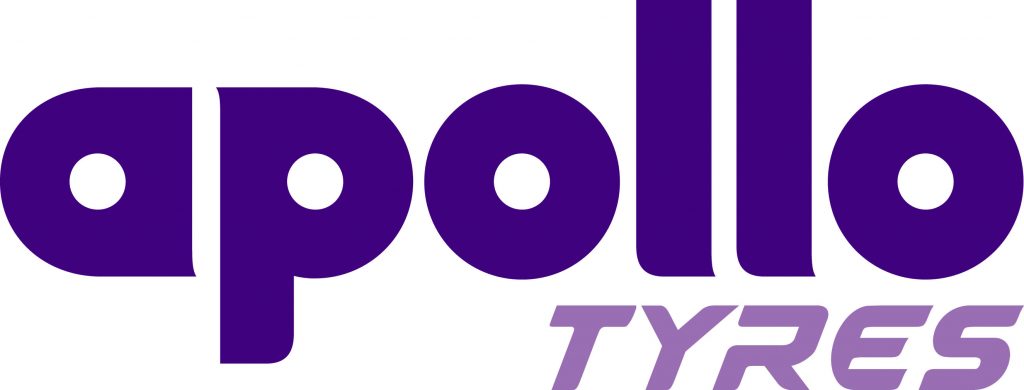
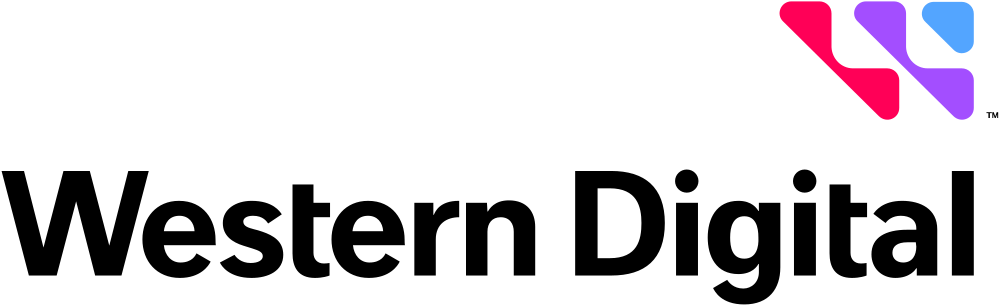
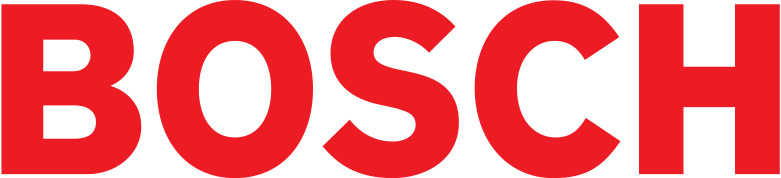

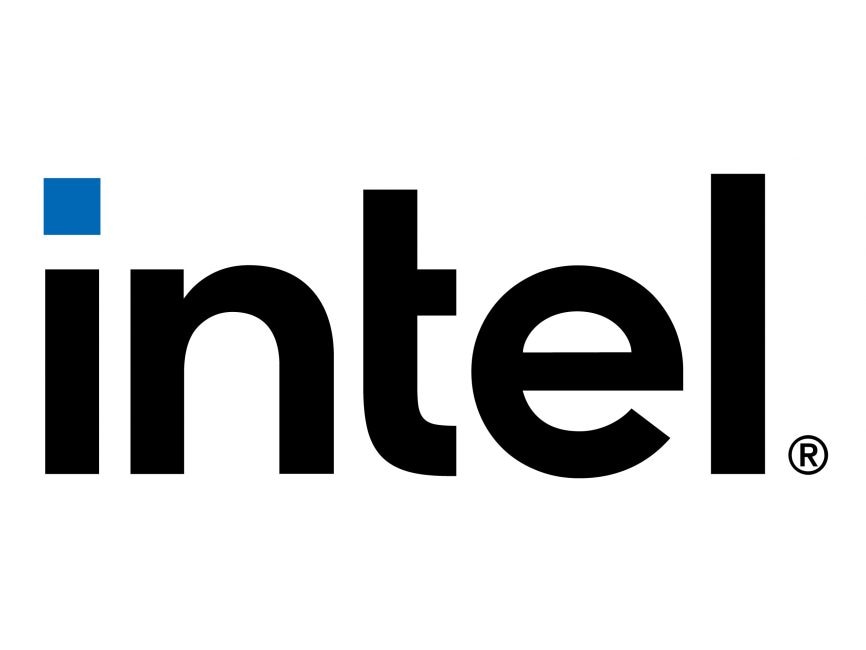

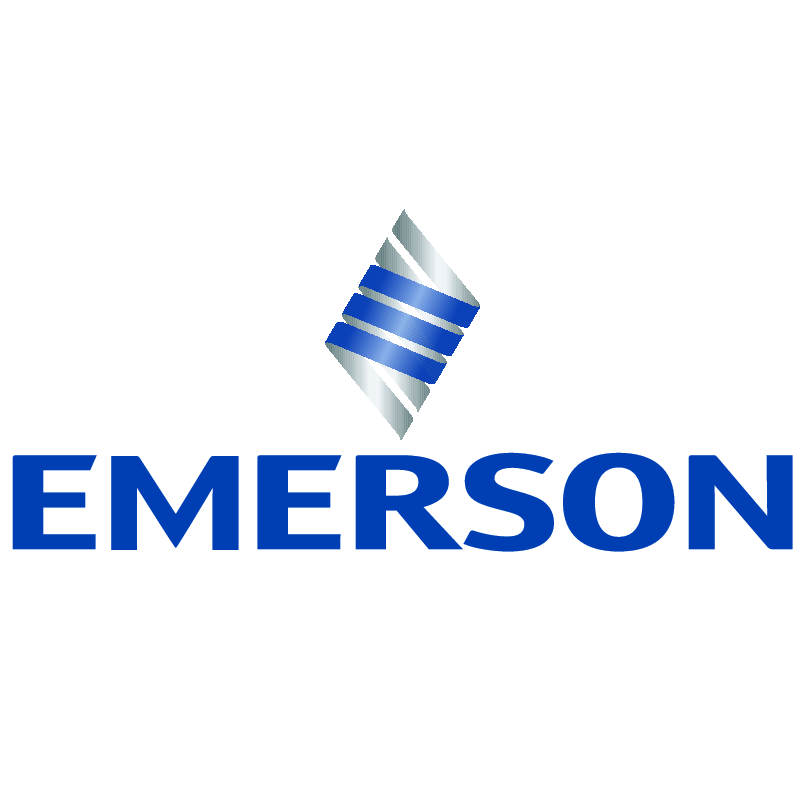
We have/had more clients than listed here, but due to NDAs we cannot reveal some of them. Ask for a personal or online meeting and we would be happy and proud to share success stories we had worked on.
The joint simulation project with EPIC InnoLabs demonstrated their expertise and helped us to optimise and understand our manufacturing processes deeper.
István Drágán
Manager Process Engineering at Vincotech
It has been a pleasure working with EPIC Innolabs. I really appreciate their depth of expertise on optimizing manufacturing, their insightful and creative thinking, their engagement and commitment to our partnership. They are willing to go that extra mile to find the right solutions for our process. Looking forward for more projects and collaborations with the EPIC Innolabs’ team !
Jhun Vitualla
Project Manager at Western Digital
A long journey becomes easy when you find a right partner. And for us EIL is one such reliable partner that is walking with us and supporting us in each step in this journey called Digitalization of Manufacturing.
Nitin Kaushik
Head Application Operations - Digital Manufacturing at Apollo Tyres
Check out some interesting cases we have worked on