Digital twins and scheduling go hand in hand in the world of Industry 4.0. A digital twin is a virtual representation of a physical asset or system, such as a manufacturing line or a piece of machinery. This digital replica can be used to simulate the performance of the physical asset, allowing companies to test and optimize its design, operation, and maintenance.
One of the key benefits of using digital twins is their ability to support advanced scheduling algorithms. With a digital twin, companies can create digital models of their production processes and use them to schedule and optimize the allocation of resources. This can help reduce costs, improve efficiency, and increase productivity.
For example, a company that manufactures cars can use a digital twin of its assembly line to simulate the production process and identify bottlenecks or inefficiencies. By optimizing the scheduling of workers, machines, and materials, the company can increase its output and reduce waste.
Digital twins can also be used to schedule maintenance and repairs, helping companies to minimize downtime and ensure that their equipment is operating at peak performance. By using a digital twin to monitor the condition of a piece of machinery, companies can predict when it is likely to fail and schedule maintenance before the failure occurs. This can save money and reduce disruption to the production process.
Overall, the use of digital twins and advanced scheduling algorithms is transforming the way companies approach their operations. By creating virtual representations of their physical assets and using them to optimize the allocation of resources, companies can improve their efficiency and increase their competitiveness in the marketplace.
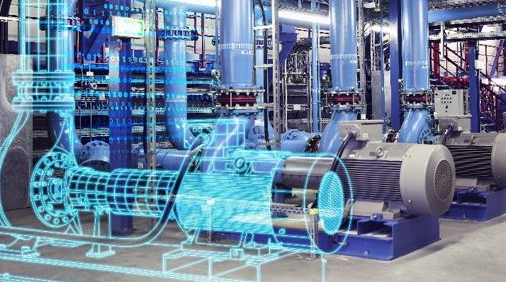